Traditie en toekomst: de fabriek van Daimler AG in Mannheim is hiervan de perfecte belichaming. Deze vestiging werd in 1908 geopend en wordt in oktober 2019 111 jaar. Hier ontstaan enerzijds uiterst moderne motoren voor vrachtwagens en bussen, anderzijds de kale carrosserieën voor alle bussen van Mercedes-Benz en Setra uit Mannheim en Neu-Ulm. Maar Mannheim is met name de geboortegrond van de grote familie van de stadsbus Mercedes-Benz Citaro. Aan de top hiervan staat sinds najaar 2018 de geheel elektrisch aangedreven eCitaro. Deze voegt zich naadloos in de productie in en ontstaat op dezelfde lijnen als de duizenden keren beproefde Citaro met emissiearme verbrandingsmotor. In de busfabriek in Mannheim werken ongeveer 3.500 medewerkers – ondersteund door talrijke machines en enkele robots maken zij van maar liefst 30.000 onderdelen een stadsbus.
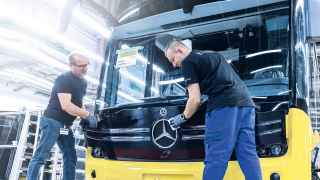
Omnibus Tijdschrift
Een bijna normale lagevloerbus
Productie van de eCitaro.
Geheel in het productieproces geïntegreerd: de productie van de Mercedes-Benz eCitaro in de busfabriek in Mannheim.
Kwaliteitsmerk Citaro: dit is het beproefde platform van de eCitaro.
Het is een cruciale bouwsteen in het concept van de volledig elektrisch aangedreven eCitaro en een kwaliteitsmerk: de beproefde Citaro is het platform van de eCitaro. Dit is een Citaro, maar wel een bijzondere. In de kale carrosserie kunnen alleen experts de verschillende soorten aandrijving van elkaar onderscheiden.
Kale carrosserie.
Van profielen en platen wordt het frame van de eCitaro gemaakt.
In gebouw 45 van de fabriek in Mannheim maken de twee ploegen van ongeveer 1.100 medewerkers van de aangeleverde stalen profielen het frame van de zelfdragende stadsbus. Hier worden eerst de profielen en platen op lengte gemaakt en afgeschuind en de metaalplaten uitgesneden. Lasersnijmachines werken uiterst precies met een snijvermogen van maar liefst 5.000 watt, dat echter precies aan de betreffende plaatdikte wordt aangepast. Afkantrobots brengen de platen in vorm, deels met meerdere afkantingen onder verschillende hoeken.
Er wordt ook veel met de hand gewerkt. Bussen zijn extreem verschillend en het aantal geproduceerde stuks is relatief laag – daarom werken de hoogopgeleide medewerkers in de fabriek in Mannheim op veel punten beter dan de robots. Mens en machine werken eveneens bij het bouwen van de kale carrosserie van een bus vaak samen, bijvoorbeeld bij kantelbare laskantelinstallaties: Medewerkers leggen profielen erin, de installatie plaatst de delen door kantelen altijd in de ideale stand en de robots lassen de delen vast. Voor de controle en kleinere nabewerkingen is dan weer de gespecialiseerde medewerker verantwoordelijk.
Indrukwekkend zijn de installaties waarin complete zijstructuren, dakframes of de onderbouw worden geproduceerd. Ervaren medewerkers leggen de geheel voorbereide vierkante buizen met de hand erin, onderbouwsegmenten komen deels uit de partnervestiging in Holysov. Nog indrukwekkender is de "dom" in gebouw 135 voor het in elkaar zetten van deze componenten, inclusief voor- en achtergedeelte. Telkens zeven medewerkers lassen bodemplaat, zijstructuren, dak, voor- en achtergedeelte aan elkaar tot een gereed dragend busframe. Daarna worden speciale onderdelen als houders en platen gemonteerd. Deze rollen, voor elke bus specifiek van tevoren klaargelegd, op setwagens mee. Alleen experts kunnen in dit stadium een eCitaro van zijn naaste verwanten onderscheiden: Deze heeft bevestigingsrails voor de latere dakopbouw, met name de accupacks. Deze constructie is afgeleid van de Citaro NGT met de gasflessen op het dak.
KTL.
Elektrostatische dompellak als betrouwbare bescherming tegen corrosie.
Nu volgt het meest cruciale onderdeel van de carrosseriebescherming: de elektrostatische dompellakbehandeling (KTL). Na een reinigingsprocedure en het fosfateren wordt het complete busframe in een zestien meter lang, vier meter breed en zes meter diep dompelbad neergelaten. Het is gevuld met 420.000 liter vloeistof. Het frame wordt daarin bijna een kwartier lang meerdere malen gezwenkt, opdat de belangrijke beschermlaag elk punt van het frame bereikt. Om ook aan de binnenkant alle profielen te beschermen, zijn deze voorzien van ongeveer 1.000 sleufgatboringen. Een fractie van deze boringen wordt later in de montage als bevestigingspunten voor aanbouwdelen gebruikt. De geheel dekkende KTL-coating is 22 micrometer dik, oftewel 22 mµ. Na het drogen bij 90 graden Celsius wordt de coating met 220 graden Celsius ingebrand. Na het aanbrengen van de naadafdichting, de bodemplaatafdichting en de montage van de eerste onderdelen gaat de eCitaro net als alle andere bussen op zijn eerste reis, hij gaat per spoor naar de vestiging Neu-Ulm om daar zijn lak te krijgen.
Montage.
Hightech-stadsbus uit het traditierijke gebouw van Benz.
De carrosserie van de eCitaro keert beplaat en gelakt terug in Mannheim en wordt dan gereinigd en gedroogd. Daarna begint in gebouw 34 van de vestiging de montage van de eCitaro. Hier en ook bij de verdere montage en afwerking zijn ongeveer 1.000 medewerkers hoofdzakelijk in éénploegendienst werkzaam. Bij en in gebouw 34 ontmoeten traditie en moderne tijd van de vestiging Mannheim elkaar rechtstreeks. De goed onderhouden baksteenconstructie heeft een klassieke en waardige uitstraling. Het stamt, zoals ook blijkt uit het opschrift, nog uit het tijdperk van Benz aan het begin van de vorige eeuw en staat onder monumentenzorg. Maar in het oude gebouw ontstaan moderne hightech-stadsbussen.
Bij de montage geldt net als bij de kale carrosserie: Alle Citaro's rollen over dezelfde lijn, alle doorlopen dezelfde productieprocessen. Alleen de werkstappen zijn anders. De werkgebieden van de hoog opgeleide medewerkers zijn dan ook complex.
In het historische gebouw groeit de eCitaro nu station voor station uit tot de geheel elektrisch aangedreven stadsbus. Op een hoog station worden componenten op het dak gemonteerd, bijvoorbeeld de airconditioning en de achterdrager met het koelsysteem van de accu's. Oranjekleurige of met een oranje beschermmantel omhulde hoogspanningskabels worden ingebracht en gelegd. Daarna volgt het leidingwerk van de dakelementen. Bij de daaropvolgende stations worden de zijruiten van de eCitaro verlijmd. Na nog meer leidingwerk in het achtergedeelte wordt in het interieur de vloer gelegd en worden de eerste componenten onder het plafond bevestigd.
Hoofdmontage.
Nu staat de eCitaro op de eigen wielen.
Het belendende gebouw 30 vormt het decor van de hoofdmontage. Hier worden de Citaro's langs twee parallelle lijnen geleid. Zo kunnen er, afhankelijk van de uitrusting, verschillende werkzaamheden bij de stadsbussen op elkaar worden afgestemd. Hoe dan ook wordt er ijverig gewerkt; vooraan, in het midden en achter zijn er medewerkers tegelijkertijd actief. Nu worden er drukluchtreservoirs geïnstalleerd en kanalen voor verwarming en airconditioning. De stadsbus krijgt elektra en bekabeling. Centraal punt is daarbij het dwarskanaal tussen cockpit en passagierscompartiment. Zowel bij eCitaro als Citaro: In elke stadsbus liggen vanwege de vele verschillende functies en lampen enkele honderden kilogrammen aan kabels. Een typische stap voor de eCitaro is het aanbrengen van de radiateur linksachter in de voormalige motortoren voor de aandrijving en de nevenaggregaten.
Dan volgt er een essentieel station: het monteren van de e-aandrijfas met de elektromotoren bij de wielnaaf. Een groot pluspunt van de as: de bevestigingspunten zijn dezelfde als die van de bekende portaal-aandrijfas van de Citaro met verbrandingsmotor. Ook de vooras wordt gemonteerd. Terwijl in de gewone Citaro de verbrandingsmotor wordt ingebouwd, krijgt de eCitaro bij het identieke station linksachter een component van vier accupacks.
Daarna wordt het interieur van de stadsbus afgewerkt: binnenplafond, luchtkanalen, de zijbekledingen van het passagierscompartiment, de cockpit en nog veel meer componenten. De bestuurdersstoel en de passagiersstoelen worden gemonteerd, evenals vasthoudstangen en scheidingswanden. Dan komen de deuren en ten slotte de voorruit.
Finishhal.
Accumontage en ingebruikneming van de hoogspanningstechniek.
En weer gaat de eCitaro naar een andere hal, nu naar gebouw 32. Ondertussen zijn de dakaccumodules van de eCitaro, net als eerder de accucomponent achterin, voorgemonteerd op het vestigingsterrein in het KEM, het competentiecentrum voor emissievrije mobiliteit. De medewerkers van het KEM zijn specialisten voor technische hoogstandjes: Hier worden allerlei emissiearme en emissievrije voertuigen als prototype opgebouwd, in kleine series gerealiseerd en wordt de latere invoering in serieproductie ervan in de productievestigingen voorbereid. De dakaccu's worden als eerste in gebouw 32 erop gezet en aangesloten op het koelsysteem, dat na een lekkagecontrole meteen wordt gevuld.
Na de ingebruikneming van het 24V-systeem, het einde van de productie is al in zicht, wijkt de eCitaro voor het eerst van het gewone proces af. In een afgezet gedeelte wordt het hoogspanningssysteem inclusief de isolatie getest en in gebruik genomen. Uiteraard zijn de medewerkers gekwalificeerde vaklieden op het gebied van hoogspanningstechniek. Omdat de accu's al opgeladen worden aangeleverd, kan het voertuig meteen rijden. Bovendien krijgt de eCitaro nu de markante dakrandverhoging, ook wordt het opladen van de accu's bij een sneloplaadstation getest.
Alle medewerkers bij de montage van de eCitaro hebben een bewustwordingstraining hoogspanning doorlopen. Maar op dit punt is er een voortgezette hoogspanningskwalificatie vereist. Alleen medewerkers met de juiste opleiding, meteen herkenbaar aan een gele stip op hun vestigingspas, hebben toegang tot dit station.
Grondige proefrit op het testtraject en de openbare weg.
Daarna komt de eCitaro weer terug in het reguliere proces. Er volgen kleinere werkzaamheden, zoals het aanbrengen van pictogrammen of de montage van de laatste bekledingspanelen. Bovendien wordt elke bus intensief getest. Tijdens de productie wordt voortdurend de kwaliteit gecontroleerd: De monteurs gebruiken daarvoor tablets, waarop niet alleen de standaardtests worden doorlopen, maar ook te allen tijde extra bewustwordingspunten kunnen worden ingesteld. Voorts nemen medewerkers bij de zogenaamde quality gates de kwaliteitsborging van de werkzaamheden nauwgezet onder de loep. Bij elke Citaro is een ritje op de remmentestbank, net als de regentest en de grondige eindoplevering, een verplicht nummer.
Maar dat is nog niet alles: elke eCitaro wordt in een proefrit zowel op een testtraject op het fabrieksterrein als op een ongeveer vijftig kilometer lang extern traject op de openbare weg getest en daarbij door de onafhankelijke kwaliteitsborging opnieuw grondig gecontroleerd. Van bedrijfstoestanden en rijfuncties tot geluidsniveau, elke afzonderlijke eCitaro wordt op deze ritten met scherpe ogen en waakzame zintuigen uitgebreid en door en door getest.
Pas daarna is hij rijp voor de overdracht aan de betreffende vervoersmaatschappij. Deze volgt naar keuze direct ter plaatse in de onderneming of bij het dichtstbijzijnde Bus World Home, op verzoek aangevuld met een bestuurderscursus of een cursus op het bedrijfsterrein van de klant. Sinds het begin van de productie met de bewerking van de vierkante buizen voor het busframe zijn er zo'n zes weken verstreken.